For all of the boat building / restoring gurus out there:
I am gutting a High Tide and replacing stringers, transom, front deck, etc. There was a lot of rotten wood and waterlogged foam from improperly sealed holes in the past.
The deck is out, the foam is out, the cap is off, and I am approximately 3/4 of the way from removing the transom. (Saving the outer skin).
My question is this. The boat feels awfully "flimsy" with all of the structural components removed, and the hull and sides don't seem too thick to me. I am getting a game plan together and will be putting things back together after the stringers are replaced. Would it be of any benefit to lay a layer of cloth (6oz or 12oz.)throughout the interior hull bottom and sides to sturdy things up a little? Or will this just add unnecessary weight and cost to the project? It appears that the hull is chopped strand, roven, then chopped strand in that order. Maybe more layers than that?, totaling around 1/4".
I am using epoxy and plan on glassing in with 12 oz biax and 6oz E-cloth. Any recommendations are welcome.
Unless the fiberglass has some sort of stress cracking, why ad the weight?
I’d keep it light - it worked for High Tide from the factory …
Thanks, Captain Ross
http://T-Topless.com folding, stainless steel T-Top fits most center console boats
http://ShadowTop.com entry level (Do-It-Yourself) T-Topless kit
http://Montauk-T-Topless.com for Boston Whaler Montauk, Dauntless or Outrage
http://Flats-Top.com Shade for Flats Boats</font id=“size1”>
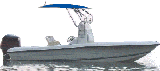
Drop your top and go T-Topless! T-Topless@RNR-Marine.com
I agree with T-topless.
A boat gets it’s strength from all components working together distributing forces. All boats feel flimsy when you remove the cap, deck, stringers and frames. That’s most of the structural support. As for the cap, picture a shoe box. Fill it about half full with sand or rocks, put the top on the shoe box and tape it, then lift it up. The box will be pretty stiff and will handle the load. Take the top off the box and try to lift it again. It will collapse.
The biggest problem you will have when stripping the hull down that far is maintaining the shape of the hull. When you remove the cap, the sides will splay out, the bow will sag and the transom will probably bow. Just like that shoebox without a lid. Now, if you were to add a few layers of glass while the hull was distorted like that, it will lock the hull into a permanent state of distortion.
I usually build some temporary frames, sometimes use ratchet straps too, support the hull bottom very good, and do everything that you can to maintain the original hull shape, or the cap will never fit the hull again. I try to do everything possible to avoid removing the cap, but sometimes they have to go, in which case I run several 2X4s across the hull, sheer to sheer and temporarily attach them before removing the cap.
You are on the right track with epoxy and 12 ounce biax. For the transom you will also need some 1708 cloth. You need to build up some thickness there and 12 ounce takes many, many layers to get enough.
Let me know if I can help, I’ve done a lot of them. Will be out of town fishing in the Gulf for the next 4 days though, so if I don’t answer, I’m not ignoring you. Will answer on return.
Capt. Larry Teuton
Cracker Built Custom Boats
Marine Surveying & Repair
I forgot to mention the 1708.
Are you going to use wood or Divinycell on the rebuild?
Thanks, Captain Ross
http://T-Topless.com folding, stainless steel T-Top fits most center console boats
http://ShadowTop.com entry level (Do-It-Yourself) T-Topless kit
http://Montauk-T-Topless.com for Boston Whaler Montauk, Dauntless or Outrage
http://Flats-Top.com Shade for Flats Boats</font id=“size1”>
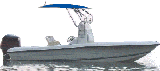
Drop your top and go T-Topless! T-Topless@RNR-Marine.com
I was going to use Coosa in place of all removed wood and structural components, but it becam cost prohibitive when everything was factored in. So now I will be using wood (sealed well)and will let er rip. Things ain’t cheap.
Wood will work fine as you will seal it well.
The high end stuff is lighter - if you want to build a super light flats skiff.
PM me if you need a price on Epoxy or glass …
Thanks, Captain Ross
http://T-Topless.com folding, stainless steel T-Top fits most center console boats
http://ShadowTop.com entry level (Do-It-Yourself) T-Topless kit
http://Montauk-T-Topless.com for Boston Whaler Montauk, Dauntless or Outrage
http://Flats-Top.com Shade for Flats Boats</font id=“size1”>
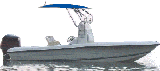
Drop your top and go T-Topless! T-Topless@RNR-Marine.com
Plenty of friendly guys on this board that are willing to go above and beyond to help you with fixing a boat. T-Top and Larry have already given very good info. If you can tell us kind of where you are, I bet one or two would even run by to give it a look and offer direct comments. You can also post pictures of the hull as it stands now. Pictures say lots more than words can. And finally, adding weight to a boat is almost NEVER the way to add strength.
I’d be happy to get a PM from you if you don’t want to post your location.
I have two questions regarding the laminating / glassing schedule of the transom and stringers.
Transom-- I have read some indication to laminate the transom plys together with thickened epoxy only (after sealing). I have also read that some would add a layer of cloth or 1708 between the plys which would also negate some of the potenial flexibility of the transom. This would also add weight however. Any thoughts?
Transom and stringers-- Which side of the 1708 (mat or cloth) goes against the outer skin, each other, finishing cloth (12 oz & 6 oz.)? Thoughts on this?
I will be using epoxy, 1708 biax, 12oz biax, and 6oz standard weave.
There is no need for cloth between the 2 layers of plywood in the transom. This was done on many boats built with polyester resin because polyester has no real bonding strength and relies on a mat layer to hold the pieces together. Epoxy has plenty of bonding strength and doesn’t need it at all. It would just add weight and material for nothing.
On the 1708, the mat layer goes to the hull skin. The biax layer to the outside of the lamination.
Capt. Larry Teuton
Cracker Built Custom Boats
Marine Surveying & Repair
10-4 Larry. Thanks for the advice. One more thought for now…
Should I try to layer the end grains of the transom core (port and starboard sides) with a layer of 6 oz cloth in addition to sealing end grains with multiple coats of unthickend epoxy?
No need for that either. Just seal the end grain with a couple of coats of epoxy before gluing. It will all get covered in cloth anyway.
Capt. Larry Teuton
Cracker Built Custom Boats
Marine Surveying & Repair
Update: I picked up a piece of 3/4" marine ply today and will be cutting and dry fitting the transom (2 pcs of 3/4" laminated together). The wood looks good but does have a bow in it (maybe an inch or two spanning the eight foot length.
How concerned should I be about this bow? Should I cut out the patterns and try to straighten them? Should I wait until I can get it close to straight? Or should roll with it as is, and just clamp the dog snot out of it once during the install?
I would go ahead and cut it out to your pattern. Cut the 2 layers with the bows opposing each other in this “()” configuration. Then when you glue and clamp, the forces oppose each other and it will straighten out. On a large transom I usually use several 1/2" bolts to clamp it together, or quite a few deck screws. Tighten from the center out, and just enough pressure to get some squeeze out. Don’t starve the glue joint. Spread the thickened epoxy evenly with a notched trowel.
When gluing the core to the transom skin, the skin often bows out. I clamp or screw a sturdy straight edge across the outside of the transom at the top, to make that skin straight all the way across, then glue and clamp the core into it. I also use bolts for clamping the core to the skin, and patch the holes later. If you are inventive you can use the engine mounting holes for clamp bolts too.
Capt. Larry Teuton
Cracker Built Custom Boats
Marine Surveying & Repair
One more tip, when you spread epoxy on those 2 layers of transom core and try to glue them together, they will act as if they are covered in grease and slide all over the place, making alignment almost impossible.
Dry fit the 2 pieces first, clamp them in place dry and drill 2 or 3 holes through them to accept a 3/8 hardwood dowel.
Take it back apart, spread the glue, knock a 2" length of dowel coated with glue into each hole, then put it back together. The dowels will keep everything aligned and will become part of the core. After the glue cures you cut them off flush and glass over them.
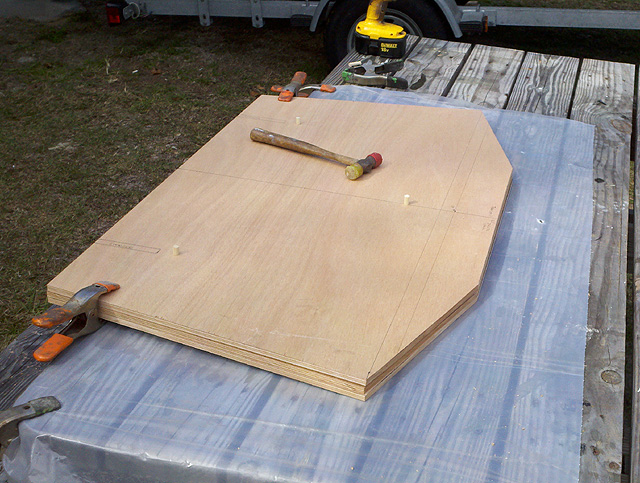
On smaller transoms I just use some weight in the center and clamps around the edges. The dowels maintain alignment. This transom is 3 layers of plywood.
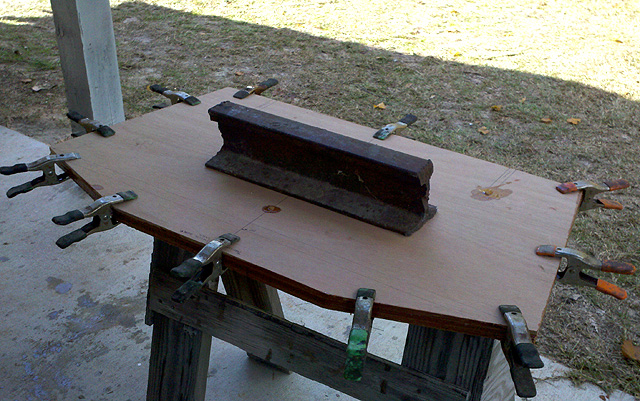
Capt. Larry Teuton
Cracker Built Custom Boats
Marine Surveying & Repair
10-4.
I cut out the two transom core pieces from my template tonight. The bow from the ply will be more than manageable once I clamp it. I will be placing the grain of the ply at opposing angles (approx 45 degrees) for any needed extra strength. A little grinding / sanding and I will be ready to laminate.
Larry, is that Meranti in that last pic?
quote:
Larry, is that Meranti in that last pic?
No, it’s BS1088 Okume. I usually use 1088 Meranti for most things, but this transom is for a technical poling skiff that I’m building for a client in Texas, and he wants it as light a possible. Using Okume will save us about 30 pounds over Meranti.
Capt. Larry Teuton
Cracker Built Custom Boats
Marine Surveying & Repair
Any thoughts on what weight cloth for floor and deck? I will be using 1/2" marine ply for floor, and either 1/2" or 3/4" for front deck…not sure yet.
For the floor, I was thinking about using one layer of 6oz cloth on underside, or should I use 12 oz.? On the top side, I am tabbing in with 1708 and I was thinking about using two layers of 12oz. biax. for the floor itself. Is this overkill / underkill? I want strength without excess weight. I will be using epoxy.
Any thoughts are welcome
quote:
Originally posted by empty pockets
Any thoughts on what weight cloth for floor and deck? I will be using 1/2" marine ply for floor, and either 1/2" or 3/4" for front deck…not sure yet.
For the floor, I was thinking about using one layer of 6oz cloth on underside, or should I use 12 oz.? On the top side, I am tabbing in with 1708 and I was thinking about using two layers of 12oz. biax. for the floor itself. Is this overkill / underkill? I want strength without excess weight. I will be using epoxy.
Any thoughts are welcome
You need to get some pics going on progress. You’ll get more interest and probably alot more good advice.
“Endeavor to Persevere.
Give,Give… Never Take.”
EC
You really don’t need any cloth on the under side, just coat it with about 3 coats of epoxy.
2 layers of 12 ounce would be overkill, as is the 1708 tabbing. I always use 1 layer of 12 ounce biax on decks and soles, it is plenty strong enough over 1/2" ply. For tabbing I would just use 12 ounce biax tape, 6" wide and skip the 1708.
1708 has a mat layer that is used when building thickness and bulk is necessary. You are just looking for strength, not thickness. 2 layers of biax tape will be stronger, weigh less and use less epoxy.
Capt. Larry Teuton
Cracker Built Custom Boats
Marine Surveying & Repair